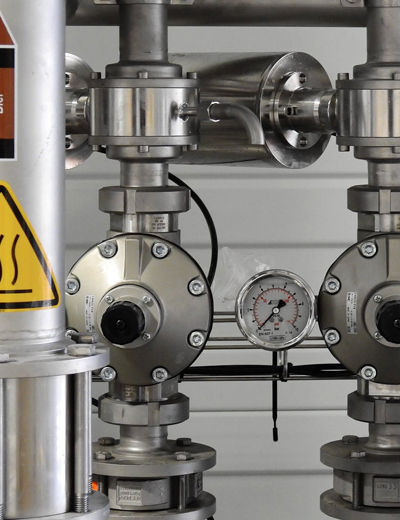
Proper maintenance and sanitation of machinery and surfaces is a critical aspect of operating any food or beverage manufacturing business. Canadians rely on the industry to provide them with clean and safe food while the workers in these operations rely on a safe working environment. The process of sanitation can be very costly between the labour involved, the energy to heat the water, the water consumption, and chemical cleaning agents used.
Many food and beverage processors have designed and constructed their process lines with a CIP or Clean-In-Place system. CIP is a setup that provides multitude of benefits including:
- Reduces employee exposure to harsh cleaning chemicals
- Saves time of disassembling equipment for COP
- Improves reliability of a consistent result using automation or set running times
The 5 most common steps to a CIP system are:
- Pre-rinse to reduce soil load
- Caustic wash with hot-water 60-85° C (140-185° F)
- Intermediate Rinse
- Final Rinse
- Sanitizing Rinse
Ozone has been used for over one hundred years to sanitize drinking water and irrigation water. So the question should be asked..."Is ozone safe for use in a CIP system?" The answer is "absolutely." Not only is it safe, ozone has several key advantages when introduced into the traditional CIP setup.
Unlike the Oxygen that we breathe (O2), Ozone is a powerful oxidant composed of three oxygen atoms (O3). The third oxygen atom in Ozone has a weaker bond, which breaks off and effectively destroys foreign bodies in water. Ozone can safely kill pathogens, micro-pollutants, microorganisms in addition to both organic and inorganic contaminants through oxidation. Ozone can be injected and mixed into a homogeneous solution to create ozonated water. The cleaning strength is approximately 1.5x that of chlorine and reacts 3000 times faster to destroy contaminants. Ozone is on the GRAS listing of FDA and accepted by Canadian Food Inspection Agency as a surface cleaner as well as food processing aid.
Because ozone converts very quickly back into oxygen, about 15-minute half-life in room temperature water, there are no residues in the piping or on surfaces. This means that the 5 steps noted above can often be reduced by at least one rinsing cycle, resulting in 20-60% water consumption reduction. The elimination of most or all chemical in the process and the reduced water use make this upgrade a sustainable, cost-effective method of improving sanitation procedures while reducing the labour and down-time associated with cleaning.
Contact us today to discuss your specific process. We will be happy to answer any questions and provide a proposed design for your operation!